
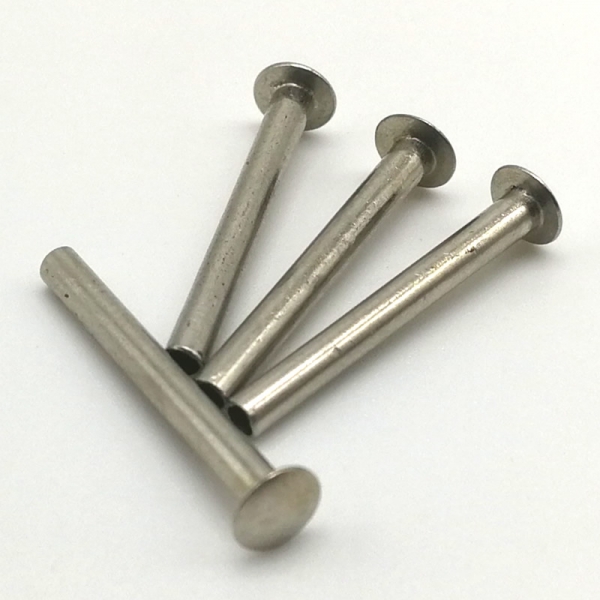
The corrosion resistance of brass lends itself to well to applications that are close to seawater.Cost-efficient multi-material design requires suitable joining techniques, ideally with low investment cost by re-using existing assembling lines. The cold forming process increases the strength of brass making it an ideal fastener for your requirements.Brass is an ideal material for use in electrical equipment due to in conductivity and for manufacturing functional items where decorative appeal is required. Brass rivets and fasteners are used in manufacturing due to their corrosion resistance, strength after cold-heading, conductivity, and aesthetic appeal.

The Valley Fastener Group produces our fasteners and rivets from a variety of customer specified grades of copper.
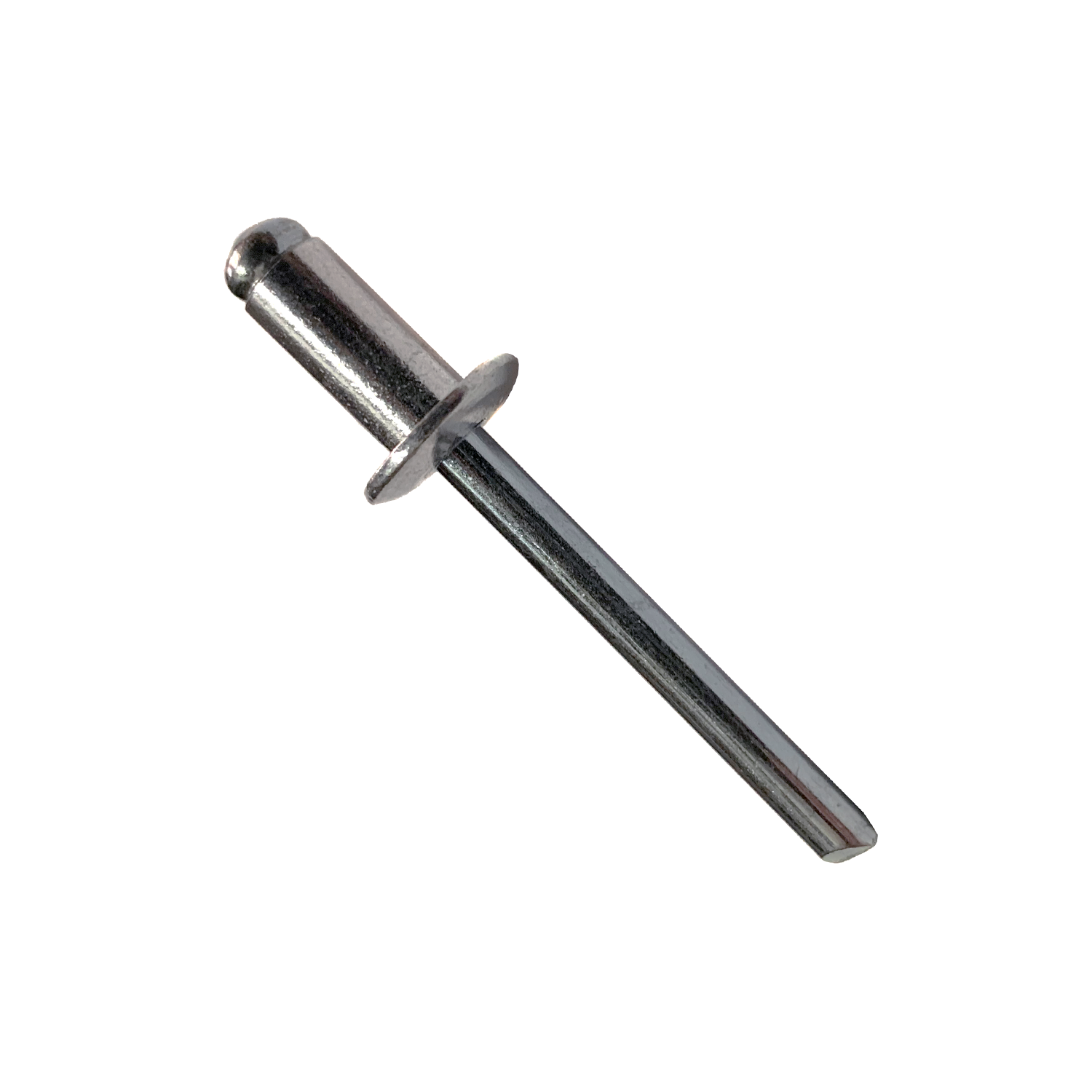
We can manufacture your copper rivets in a variety of sizes and thicknesses – copper rivet options range from semi-tubular rivets, solid rivets, self-piercing rivets & more. Copper rivets are commonly used in clothes, saddles, shoes, belts, bags and more to reinforce the product and because of how aesthetically pleasing copper rivets look.
#Metal rivet series#
VFG produces our rivets and fasteners from a variety of customer specified grades of CHQ Aluminum Material including 2024-T4, 2011-T3, 1000, 6061 as well as the 50 series aluminum alloys. Aluminum provides strong corrosion resistance and is ideal for many applications.Additionally, the formability of most aluminum material is excellent, so producing complex part configurations is often possible. Known for being soft and lightweight, aluminum continues to be one of the most common material choices for rivets and fasteners.The chemical composition also determines the work hardening rate of the material during production and any additional cold working of the part (clinching) in order to fasten it into your assembly. The chemical composition of each alloy determines the amount of the forming pressure that is required to produce the part. The corrosion resistance, mechanical properties and cold formability of stainless steel rivets, fasteners, and part designs are all important engineering considerations when selecting these fasteners.Long-lasting strength is a primary trait of carbon steel parts. Screws and other cold formed special threaded fasteners typically are specified using higher carbon steels than the most common rivet materials. Higher carbon steel parts work-harden more when they are produced and work harden again as they are clinched or upset in your application.The steel raw material used to produce our rivets and fasteners have excellent formability. Low carbon steels are most often selected for rivet applications that primarily require good part formability so they can clinch over or upset well in your application.When higher carbon steels are specified for rivets and fasteners, the strength and hardness of the material increases and the formability of the material decreases.Want to learn more about rivet and fastener materials or have a question? Contact us today for your rivet material needs! We suggest that you choose a material that has the same mechanical properties as the pieces and parts that you are joining together. VFG is able to provide metal fasteners and rivets made for a multitude of applications that supplies every industry with exactly what you need. VFG carries a multitude of different rivet materials to meet the needs of various applications. Our rivet materials are made out of steel, stainless steel, aluminum, brass, and copper. In addition to Valley Fastener’s extensive inventory of metal rivets, fasteners, and pins, VFG offers these products in a wide range of metal materials.
